Quality Control In-line on the plant
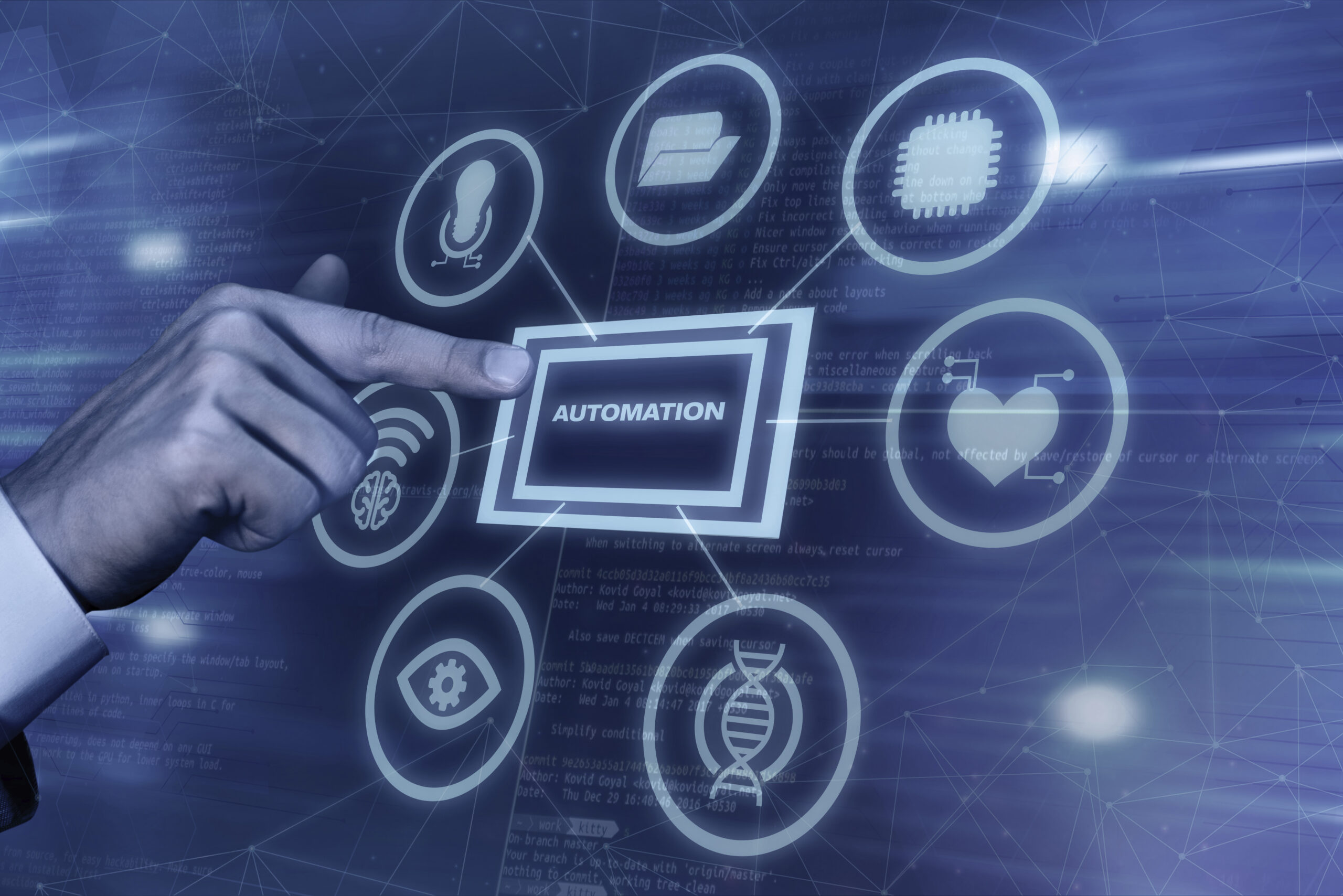
Why today do we still see especially with liquid products operators walking down the site to the laboratory with a 200ml sample for testing.
Of course, there will be tests that can be carried out only in the laboratory but many test such as pH and specific gravity can be measured on the plant.
The 200ml sample or equivalent has been with us for many decades as it was and still sometime is thought only the correct testing can be done in the laboratory.
The Japanese taught us quality control on the plant, the automotive industry embraced it. Build in quality, teach the operators about quality and how to measure it.
In my early days working in the chemical plants, technology had not evolved to allow in-line testing but I embraced the concept of “on plant” testing. This saved time and operators embraced the concept. Taking a pH test to check before proceeding to the next stage was quick and easy. If OK they had probably saved 30 minutes or more production time by not having to walk to the laboratory and wait for an available chemist.
Some laboratory methods required at first a set temperature to test the specific gravity but later we learned to graph the temperature profile and Specific Gravity (SG) to speed up Laboratory time and thus reduce plant idle time waiting for results. Eventually meters and testing equipment became available to allow SG in-line.
These are only two examples but so often required and yet still operators walk long distances and wait for a chemist to perform a test that can be done on the plant automatically.
OK, Plant software has to be updated with a new version allowing the Quality control element and this is a cost. But payback is in reduced production time leading to increased available capacity. Plus you are not testing only 200ml, you are running a predetermined amount through the testing process of many litres.
If you are interested in upgrading your plant to have include in-line testing contact us: Contact
Comments are closed.